The matrix below details the areas in robotics where automotive companies should focus their time and resources. We suggest that automotive manufacturers invest in technologies that are shaded in green, explore the prospect of investing in technologies shaded in yellow, and ignore areas shaded in red.
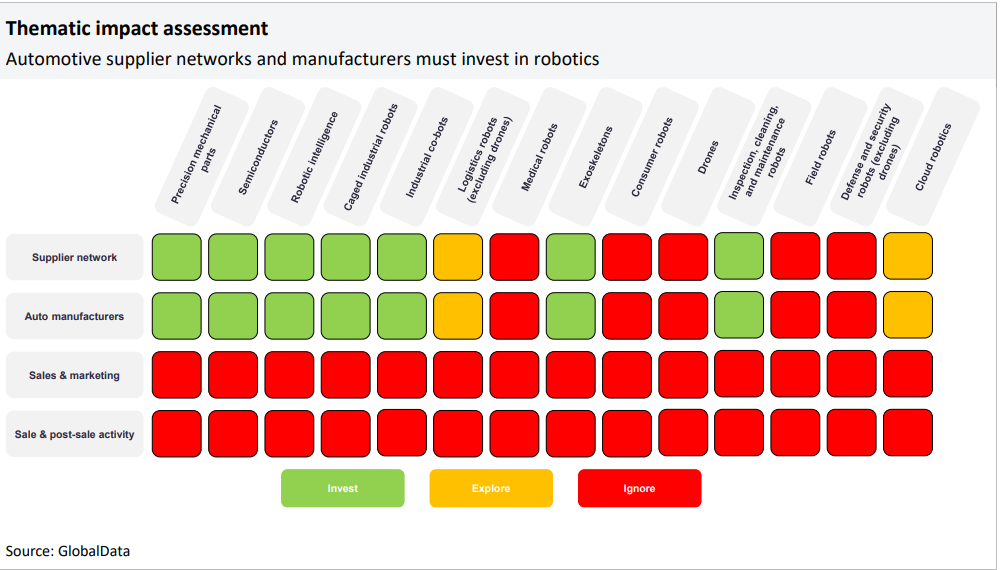
Robots, as we know them, are a 20th-century creation. However, the idea of automata or mechanical devices built to replace human labour on physical tasks is much older. Examples go back to ancient Egypt, Greece, and the Roman Empire. The first known case is from Egypt around 3,000 B.C., when human figurines were built into water clocks to automatically strike the hour bells.
The importance of robotics in the automotive sector has surged in the last century. In 1913, the term “Fordism” was named after Henry Ford; Fordism not only refers to post-war economic and political growth, it also is used in reference to mass production of goods on an assembly line. Some five decades later, General Motors adopted Devol’s Unimate in 1961, the world’s first industrial robot.
And now, robotics is a theme without which the world cannot live. In the automotive sector, GlobalData recommends investments in precision mechanical parts and exoskeletons. This machinery can enhance human performance by allowing limb movement with improved strength that can help lift heavy objects. Caged industrial robots have already taken off in Chinese automotive markets. Industrial co-bots, logistics bots, and inspection bots can improve efficiency and safety for automotive manufacturing and suppliers. And lastly, semiconductors are important for automotive manufacturers as chips are vital for robot systems and vehicles.
How robotics helps address supply chain disruption
While adopting robots cannot fix the issues across the automotive supply chain, they can speed things up drastically, ensuring high output in a short amount of time. Robots can aid in the assembly of vehicles by improving throughput and assisting in keeping up with demand. The initial manufacturing stages include welding, handling, and assembly, while later stages include robotic painting, finishes, and machine vision-quality control.
During the early automotive manufacturing stages, robots are excellent facilitators around automating the welding process. Robots can efficiently weld heavy and bulky parts together, which would be difficult for humans. Arc welding and resistance spot welding are both common applications of robotic welding. Arc welding uses heat to melt and thus weld parts together, while resistance spot welding is more specifically used to weld several different parts.
According to Robots Done Right, arc welding accounts for about 50% of all robotics applications in the automotive sector. Robotic welding is a major application in the automotive sector due to its ability to improve throughput, accuracy, and repeatability while making the production process safer and more efficient. Robotic welders and handlers must collaborate to keep the assembly line moving so the welding robot can perform all the programmed welds.
Robots can also be used to support part handling and transfer. Working with vehicle parts is associated with several risks for employees. They could be exposed to items with extremely sharp edges, molten metal, and excess weight in the production line that could cause injury or death.
Robots are the perfect solution to mitigate these risks, as machinery can be exposed to these hazards with relatively little risk. This can speed up the handling process and reduce the risk of accident and injury claims by omitting the need for employees to work in dangerous environments.
As vehicle parts are welded together, robots can also be used to automate the assembly line for automotive manufacturers. Adopting robots allows the assembly line to be reliable and timely without causing any disruption to the vehicle production cycle.
As vehicles go down the assembly line, various mundane, repetitive, but vital tasks, including installing windscreens and tire mounting, can be consistently done at high speed with precision and accuracy that would be difficult for a human workforce to match.
General Motors, Hyundai, and Ford are currently trialling exoskeletons. Exoskeletons and robotic hands are designed to be used by staff and provide support for manual work such as drilling and overhead work. However, these wearable machines also can provide workers with additional strength and allow assembly line employees to complete their shifts while reducing fatigue, strain, and injury.
Following the initial stages of robotic vehicle assembly, robots can also be used to paint vehicles. Robotic painting has been used for decades. Early paint robots were hydraulic and, though still in use, they can produce streaky finishes and let off toxic fumes. Modern paint robots provide a consistent coat to vehicles' entire exterior and interior bodies.
Machine vision can also aid quality checks, particularly for cosmetic, optical inspection. Machine vision works by using an algorithm-based camera or laser that matches goods and provides feedback. If the algorithm fails to match the good to the required standard, the part will be prevented from moving further down the assembly line as it is likely faulty.
Machine vision in robotics typically picks up on edge detection, pattern recognition, and colour analysis. Machine vision is a key tool for quality control as it flags products that do not meet manufacturer requirements and prevents defective products from reaching the point of sale.
However, companies must apply robotics cautiously. General Motors is well known for its robotics adoption, but the company experienced significant disruption to its supply chain in the 1980s, when regularly malfunctioning robots spread paint across the plant and broke materials. The firm could not produce goods as quickly as it wanted, and suffered due to an inability to distribute its products. While the innovative use of robotics in the automotive sector is encouraged, a lack of preparation and research before tech implementation can put additional strain on supply chains.
How robotics can mitigate labour shortages
In 2022, Jeff Burnstein, president of the Association for Advancing Automation, said, “robotics could help reverse productivity declines and fill repetitive jobs human workers don’t want.” Following the Covid-19 outbreak and supply chain disruptions, there are shortages of workers available to work in manufacturing.
Robotic automation is a way to reduce the dependency on human workers in manufacturing. This will be most evident in mature auto markets, including the US, Europe, Japan, and South Korea. In Japan, the aging population is a major challenge. As labour shortages make it harder to find skilled professional workers, robotics provides a solution as their use in the automotive sector reduces the need for human intervention.
How robotics can support government incentives
As governments worldwide push for greater use of electric vehicles, the automation of the automotive supply chain can aid demand. As of June 2022, in the US, the Biden-Harris Administration proposal “activated the purchasing power of the federal government to procure 100% zero-emission light-duty vehicles by 2027 and all vehicles by 2035”. In the UK, the government has introduced £300 million ($366 million) in grant funding for sales of electric vans, taxis, and motorcycles to boost the drive to net zero.
The European Commission aims to have 30 million electric vehicles on Europe’s roads by 2030, up from 1.4 million in 2022, with 1 million electric and hydrogen vehicle charging stations to be installed by 2025. The adoption of robotics in the automotive sector can help meet the high demand for new vehicles by providing a quick and consistent manufacturing output.
Robotics’ role in worker health and safety
While robots have been widely adopted in the automotive industry and can increase employee health and safety, the maintenance and adoption of robotics should be closely observed, as robotics is also a source of safety hazards in the workplace. In 2015, a robot was involved in the death of a worker at a Volkswagen production plant in Germany. The 22-year-old was part of a team setting up the stationary robot when it grabbed and crushed him against a metal plate. Therefore, companies that wish to adopt robotics must tread carefully and ensure safety measures and precautions are implemented to ensure employees face minimal risk.
GlobalData, the leading provider of industry intelligence, provided the underlying data, research, and analysis;used to produce this article.
GlobalData’s Thematic Intelligence uses proprietary data, research, and analysis to provide a forward-looking perspective on the key themes that will shape the future of the world’s largest industries and the organisations within them.