Feature
Robots versus garment workers
Will robots one day be able to take over almost all production steps in clothing manufacturing? Jens Kastner investigates.
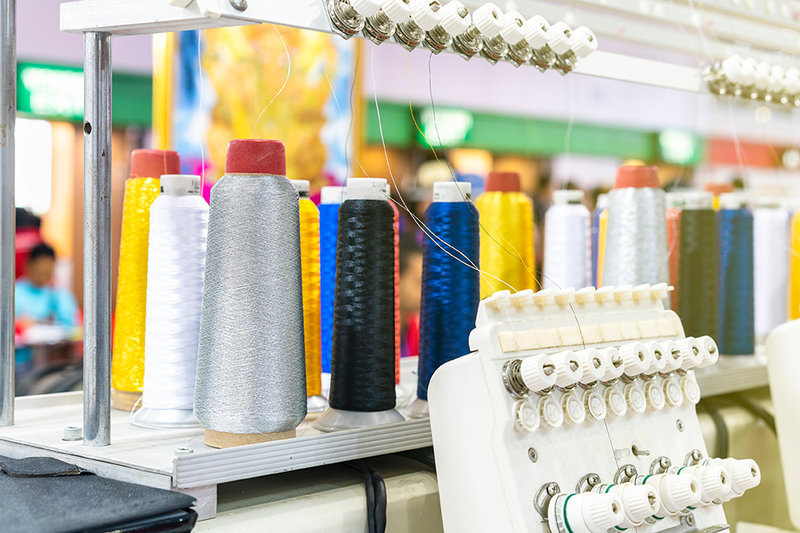
Most of the textile industry is 40 years behind compared to the level of automation technology that is available today. Credit: Shutterstock.
Research and development has been making major progress in the handling of limp objects such as fabric – a key challenge to the automation of the clothing industry. However, the clothing industry is still far from widely adopting robots, as a range of technical and economic realities are still working against these technologies.
Speaking to Just Style, industry experts agree that humans with their haptic abilities, such as when guiding fabric along a sewing machine or readjusting its position, cannot be easily replaced. On the other hand, there is in many manufacturing centres a growing need for automation due to a lack of skilled workers willing to work in the sector.
“The handling of individual bobbins is already widely done by robots, as bobbins are rigid bodies and can therefore be gripped in the same way as objects made of metal or wood,” said Falko Schubert, a research associate for robotics and automation at the Saxon Textile Research Institute (Sächsisches Textilforschungsinstitut - STFI) in Germany.
He told Just Style “the handling of individual layers of fabric and insertion into machines can already also be done by robots, as shown by Robotextile,” referring to a Germany-based company that developed textile grippers that use either air flow, adhesion or rubber rollers to pick up individual layers of fabric from a pile and arranging them according to a preset plan.
By contrast, Schubert sees robotised sewing as still needing a lot of development due to remaining hurdles in the integration of sensors and camera/image processing for position detection and adjustment of the textile: “While I believe that this will be sorted out at some point, I believe the handling of individual threads will never work,” Schubert said.
Michael Fraede, Robotextile’s CEO, agreed with Schubert’s assessment, adding that robots have already mastered the clearing of textile cuts in single layers from the cutting table. Fraede sees the laying of two matching textiles on top of each other to be sewn together as a task that will be mastered soon.
“The removal of blank stacks from the cutting table will come eventually, whereas we will never see all human haptic abilities on the robot at the same time,” Fraede said.
Garment sector’s lack of automation technology
Despite this, according to him, much of the textile industry is 40 years behind the potential level of automation technology available today. For companies wanting to automate, as a result, Fraede recommends avoiding wholesale automation, choosing rather the introduction and the development of competence to be carried out carefully and step by step.
“At the beginning, the handling of secondary activities should be automated, as these activities are boring and do not add value, making workers want to quit their jobs,” he said.
Dr Susanne Bieller, general secretary of the International Federation of Robotics (IFR), confirmed to Just Style that the IFR is closely watching promising companies that focus on robots for limp objects such as textiles. As for noteworthy examples, she singled out Robotextile, fellow German company sewts and US-based SoftWear Automation.
While sewts has been developing cutting-edge machine learning and computer vision technology to enable highly intelligent gripping operations that are already used in industrial laundries, SoftWear Automation’s Sewbots use a combination of patented high-speed computer vision and lightweight robotics to steer fabric to and through the needle with, as the company claims, greater speed and accuracy than a human.
Meanwhile, Sewbo takes a very different approach by temporarily stiffening fabrics, allowing off-the-shelf industrial robots equipped with suction cups to easily separate and pick up single fabric layers, just as if they were working with sheet metal.
Sewbo claims that the fabric panels can be easily molded and welded before being permanently sewn together. The water-soluble stiffener is removed at the end of the manufacturing process with a simple rinse in hot water without needing detergents, leaving a soft, fully assembled piece of clothing. The stiffener can then be recovered for reuse. The treatment uses polyvinyl alcohol, a non-toxic polymer that is already used elsewhere in the textile production process, as a ‘sizing’ that temporarily strengthens yarn during weaving.
Delving deeper into the economic considerations, Anton Schumann, a partner at textile consultancy Gherzi, observed that while robots have already gained a firm foothold in the high-volume production technical textiles and bedding, they have not done so in the production of underwear and shirts.
“Although the likes of Amazon, Uniqlo, H&M and Decathlon are already using robots for long seam sewing, folding, gluing, heat-sealing and packaging, these processes are still done mostly in combination with human workers and only for production of very high-volume batches,” said Schumann.
“One exception coming to my mind is orthopedics garments, as that sector is suffering from a lack of certified personnel across Europe, with start-up ADOTC serving exactly that market.”
ADOTC, whose acronym stands for ‘Another Dimension Of Textile Configuration’ has developed digitally networked robot sewing cells, which in future will sew clothes and domestic fabrics, medical and technical textiles automatically. The ADOTC concept includes all the components for total automation, from the interface through to the robot technology and finally the sensors and grippers -integrating an app with dashboards to enable real-time production monitoring.
In the immediate future Schubert predicts the major robot-related breakthroughs for textile-garment business cases might be related to the automisation of data. He stressed how recent years have brought robust progress in the usage of artificial intelligence for order and turnover prediction, handling of customer complaints and supply chain fulfillment.
“There is great demand for such technology, as the old business model of ordering 10 containers of shirts from Bangladesh and making enough profit by selling four of them while discarding the remaining six to the landfill is no longer sustainable,” he said, and added: “The trend is toward smaller batches for which you need accurate digital forecasting, which only robots with their algorithms can deliver.”
Twenty years ago, the cost of implementing RFID tags and the ecosystem (software) was much more expensive than today.
Franck Germain, VP marketing at Linxens
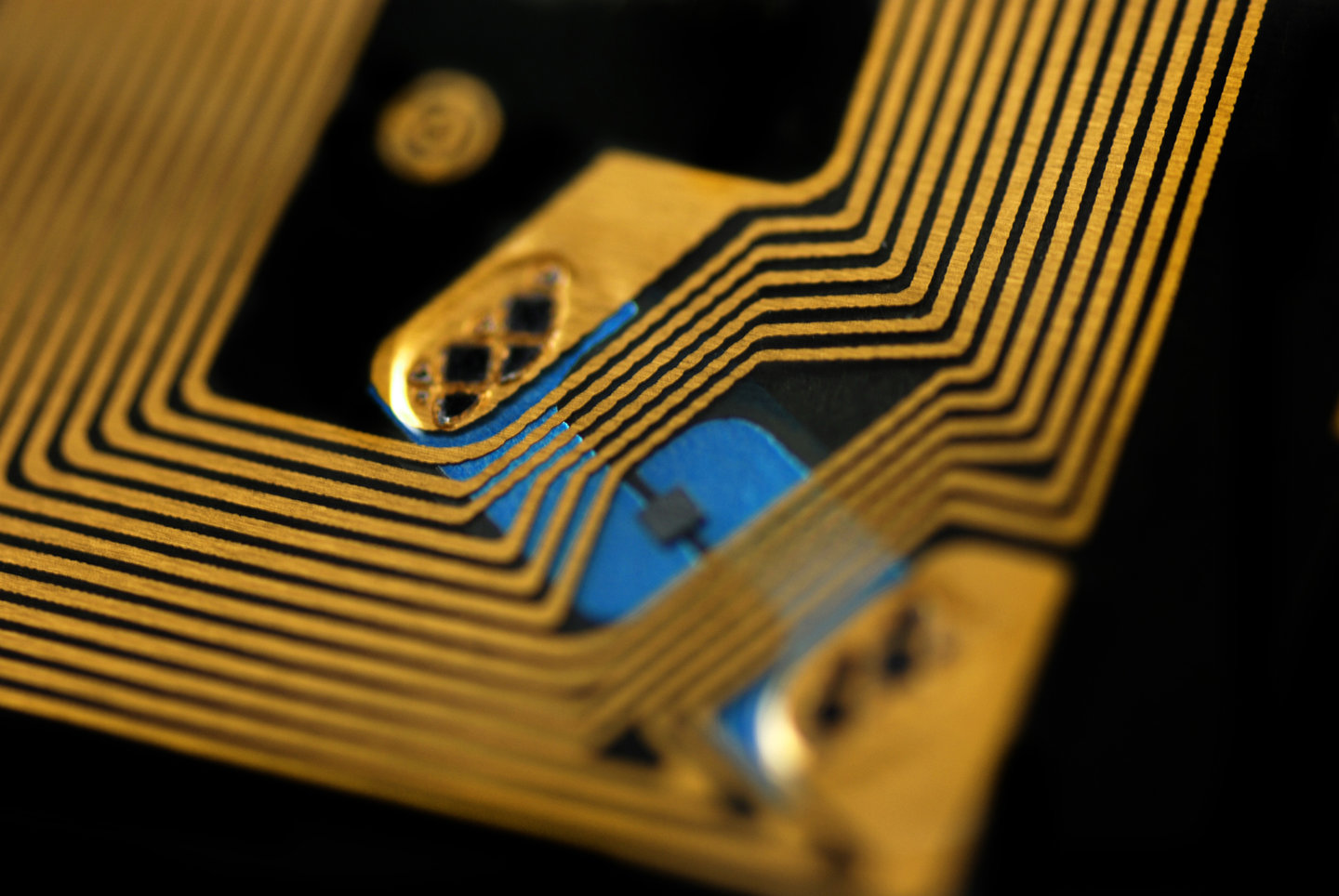
Credit:
In recent times, various global administrators have issued regulatory standards. The US Food and Drug Administration (FDA) has provided guidance for the use of RFID in the drug supply chain and to standardise the data format. In the US Drug Quality and Security Act (DSCSA), the FDA mandates that manufacturers and trading partners should have full interoperable electronic track and trace systems in place by November 2023. The European Medicines Agency (EMA) has produced similar recommendations, but with a focus on using RFID tags to track the movement of drugs through the supply chain, and instructed companies to implement appropriate security measures to protect patient privacy and prevent counterfeiting.
GlobalData, the leading provider of industry intelligence, provided the underlying data, research, and analysis used to produce this article.
GlobalData’s Thematic Intelligence uses proprietary data, research, and analysis to provide a forward-looking perspective on the key themes that will shape the future of the world’s largest industries and the organisations within them.